Printed Circuit Boards
PRINTED CIRCUIT BOARD wet processing systems are our specialty.
The vast majority of automated lines we’ve installed over the last 20 years have been for printed circuit boards. At the time of the pwb industry’s precipitous fall, in 2000-01, BTA was the leading U.S. supplier to what were considered “Tier #1” board companies, i.e. Sanmina, Tyco, DDI, Rockwell-Collins, etc.
Unlike its competitors, BTA will not force-fit you into a line which we’ve built previously for others. Our diverse range of hoist systems allows us to be highly objective when determining the best system for your needs and footprint.
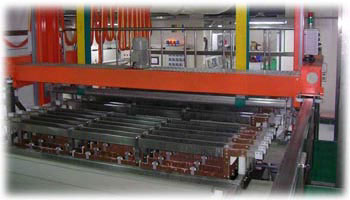
BTA’s success in the PWB field can be attributed to the following:
• High quality, robust, stainless steel mechanical equipment offered at competitive prices
• Unique, highly flexible optimizing/scheduling control systems with capabilities NOT available from any other U.S. of foreign source.
• Professional Project Management staff to insure information flow and proper system coordination.
• Pulse Plating Systems’ Expertise (equipment and chemical), enabling BTA to guarantee a level of plating performance not available from any other plating equipment firm. WST is our own, proprietary, multi- frequency, complex waveform pulse system, and is used throughout North America and Asia by firms such as:
TTM, DDI, Sanmina, Elec & Eltek, Multek
Rack Plating Systems
Our equipment offerings for RACK PLATING are the most diverse in the industry!
Unlike competitors with limited product designs, since 1995 we’ve successfully integrated equipment and technology from our long-term
Strategic Partners into our designs and systems. With a significantly broader range of products, we objectively determine the appropriate and cost effective solutions for your particular needs.
BTA has "NO AXE TO GRIND" in the flexible way we approach your Rack System needs and budget.

Rack Equipment Solutions Include:
•
Stainless steel "mini" hoists **
• Steel and Stainless Cantilevered (Side-arm) hoists **
• Steel and stainless railrider hoists
• Overhead cranes
• Carousel, RTMs (Return Type Machines)
**available with environmental enclosures
Energy-conserving designs are a specialty.
By minimizing losses from heated tanks, and dramatically reducing exhaust cfm (often by more than 80%),
we deliver
significant savings in
recurring heated make-up air and energy consumption, especially in Northern U.S. & Canada.
Integral to the system’s success is state-of-the-art controls.
For more than 20 years, we have exclusively utilized AUCOS control systems. All systems are available with:
• Flexible, Production-Scheduling/Optimized Controls
• Advanced real-time simulation/verification of layout and capacities.
• Optimized concurrent processing of widely varying process recipes and dwell times. Unlike less intelligent “dynamic scheduling systems”, there is no need for part/fixture storage or queue.
• Superior, in-depth fault diagnostics.
• Global, modem service (PC front-end & PLC), available 24/7
• Extensive part database, enhanced control & traceability
• Available in UNIX, LINUX & Windows platforms.
• High accuracy infra-red & laser hoist positioning systems
Barrel Plating Systems
Our equipment offerings for BARREL PLATING are the most diverse in the industry!
Unlike competitors with limited product designs, we’ve successfully integrated equipment and technology from our long-term
Strategic Partners into our designs and systems. With a significantly broader range of products, we objectively determine the appropriate and cost effective solutions for your particular needs.
BTA has "NO AXE TO GRIND" in the flexible way we approach your Barrel System needs and budget.
Barrel Equipment Solutions include:
• The patented
PLATEXPRESS™ System which is unique in it's ability to provide a more consistent finish with lower operating costs.
• The HYBRID System, which utilizes many of the PLATEXPRESS
™ features, but with traditional barrel/hoist orientation.
• Stainless steel "mini" hoists **
• Steel and Stainless Cantilevered (Side-arm) hoists **
• Steel and stainless railrider hoists
• Overhead cranes for high capacity, double barrels
**
available with environmental enclosures
Water-conserving “Multi-Rinses”™ reduce floorspace and water consumption by >50%. These have been used for years within U.S. “HYBRID”installations. These lines require only a single rinse station on-line, in lieu of 2 and/or 3 station counterflow rinses, thus shortening the line footprint & number of hoists required.
IN-BARREL DRYING- a time-proven, patented system used for years in the U.S. Unlike conventional, centrifugal drying, more delicate parts need not be dumped into spin baskets for placement inside the dryers. Rather, following final on-line rinse, barrel is conveyed to semi-vacuum dryer stations with special, minimal rotational cycle. The barrel dryers are available with automatic covers, to minimize energy losses.
Integral to the system’s success is state-of-the-art controls.
For more than 20 years, we have exclusively utilized AUCOS
control systems. All systems are available with:
• Flexible, Production-Scheduling/Optimized Controls
• Advanced real-time simulation/verification of layout and capacities.
• Optimized concurrent processing of widely varying process recipes and dwell times. Unlike less intelligent “dynamic scheduling systems”, there is no need for part/fixture storage or queue.
• Superior, in-depth fault diagnostics.
• Global, modem service (PC front-end & PLC), available 24/7
• Extensive part database, enhanced control & traceability
• Available in UNIX, LINUX & Windows platforms.
• High accuracy infra-red & laser hoist positioning systems
Platexpress
PLATEXPRESS, a recently patented method for barrel plating facilities that eliminates many drawbacks of more conventional barrel systems, enabling one to:
• Significantly increase throughput without additional hoists, and the reduced efficiencies that come with lines having large numbers of hoists in-line.
• Improve the uniformity of plating distribution on all the parts within the barrel.
• Minimize the distance between anode and cathode, thereby reducing energy consumption, with no risk of collision during barrel insertion.
• Eliminate the need to drag a barrel over others with the consequence of highly concentrated and corrosive substances deteriorating the underlying barrels, exhaust hoods and anode bars.
• Minimize the fumes from barrels once travelling outside of a tank.
• Reduce the machine footprint
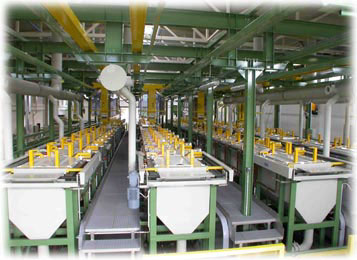
PLATEXPRESS System Benefits:
• Higher production vs. traditional plating lines with same operational conditions.
• Faster deposition and improved distribution.
• Lower electrical power consumption.
• Reduced energy (heating) costs.
• Lower solution dragout.
• Water consumption and floorspace requirements reduced by >50%.
• Reduced maintenance costs.
• Lower exhaust emissions and recurring cost of make-up air.